Needle Punched Non Woven for Filtration
How they are manufactured
Nonwoven fabrics are manufactured by binding together small fibers. These fibers are bonded together either mechanically (needle punching), thermally or chemically. Out of all these processes Thermal Bonding is the most commonly used process for the manufacturing of Non Woven Fabrics.
Next is the process of Mechanical Bonding in nonwoven manufacturing. This type of method in nonwoven production is also widely used. This method of binding fibers is accomplished through three ways. Needle Punching Technique, Stitch Bonding and Hydroentanglement. Here we will talk about the needle punched non woven fabric.
Needle Punching Technique
Needle Punched non woven fabrics are produced by punching a range of needle directly on the web. Punching needles into the web makes the felt quite flexible, having distinctive pores. These pores makes this non woven felt a perfect fit to be used for filtration and drainage. It increases the ventilation of the fabric.
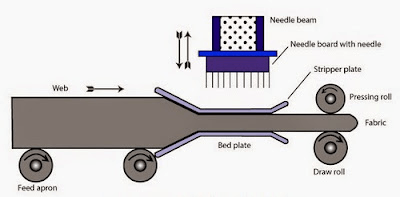
Variations in Punching Technique
The process of punching the needles into the fibers depends and vary as per the requirement and its applications. So it is quite versatile. But Carding them is a limitation. As some of the fibers could not be carded well in the machines. Choice of fibers for needle punching technique is also very important. As the fibers need to be thermally resistant to high temperature, chemical resistant and abrasion resistant.
Moreover there are various other aspects also that influence the performance of the needle punched staple fibers. It is directly and proportionately related to the type of fiber being used i.e. polymer, fiber density, lubrication, diameter, dimensional stability, length, quality, needle density and depth of penetration of needle, fabric porosity, thickness and fabric permeability.
Needle Punched Nonwovens for Filters
Needle Punched technique makes the nonwovens worthy for usage in the manufacturing of filter media. Calendaring also plays a positive role in improving the filtration property of developed non woven fabric. High the quality of fiber more will be the strength of non woven but on the other hand it will decrease the punch density of it. Similarly the air permeability is inversely related to the punch density and proportion of high quality fibers.
Effect of Calendaring on Filtration properties
In the manufacturing process calendaring is a process that provides a smooth texture to the fabric, finishes it and gives it a thinner physique by compressing it. This process is accomplished by passing a continuous sheet of fabric through a number of heated rolls. The combination of rolls is called Calendars. When the non woven fabric is passed through calendars it gives it a lustrous look and glossy finish.
Conclusion
The above summarized knowledge about needle punched nonwovens shows the applications of this fiber as filter media, the technique being applied to make a plain non woven a needle punched non woven and its positive applicability and outcomes.
The use of non wovens is so much around us yet we are not able to differentiate and understand sometimes the uses where they have been put to serve the basic purpose. This Industry is supposed to see a high rise in the coming future considering the widespread knowledge among human beings about its positive outcomes.